Trim waste in instrument reprocessing with these simple steps.
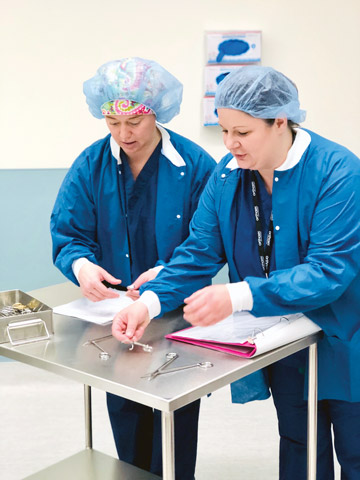
PICK AND CHOOSE Sterile processing techs who analyze the trays they receive are well-positioned to identify what's really needed for each case.
If you're looking for low-hanging fruit for cost savings at your surgical facility, look no further than your sterile processing department (SPD). "Your certified sterile processing techs are the gatekeepers for the instruments that end up in your ORs," says Alicia Apostoles, RN, BSN, MSN, MBA, director of ambulatory surgery development for OrthoNY Surgical Suites in Albany, N.Y.
"There's perhaps no one in your facility who's more dialed into which tools are needed, and which aren't, for every case your surgeons perform," she adds. "Tapping into their in-the-trenches insights will help you find cost-saving opportunities and improve your facility's bottom line."
Ms. Apostoles offers these three suggestions for finding savings in your SPD:
- Rightsize your trays. Have your SPD techs receiving case carts analyze the items surgeons did and didn't use, as it might be possible to create smaller trays. Ms. Apostoles proudly points to her own facility as an example. Her SPD techs worked with an instrument vendor to consolidate total knee instruments from six trays to two, eliminating about 100 instruments to save $320 per case in reprocessing costs. This single step enabled the facility, for each total knee case, to decrease sterilization cycle times by 30 minutes, run one sterilizer instead of two, reduce time to apply blue wrap to sterilized instruments from 45 minutes to 15 minutes, and save money on blue wrap, tray liners and chemical integrators. "Because of the techs' problem-solving, we're able to schedule back-to-back cases and keep the surgical schedule on track without having to purchase thousands of dollars in additional instruments," explains Ms. Apostoles.
- Improve management of loaners. Have your SPD techs create and manage a sign-in policy for vendors bringing in loaner instrument sets that requires all trays and instruments be on site and signed in at least 48 hours before the start of the case in which they'll be used. This enables SPD to make sure all needed items are present and reprocessed before the scheduled case, as well as spot waste-reduction opportunities by pulling unneeded instruments, says Ms. Apostoles. This policy holds instrument vendors accountable for the accuracy of their sets and can help consolidate instruments.
- Tap into your techs. When you add new procedures, include SPD techs in related surgical staff training and in-services. Allow them to see the instruments that will be used and how the table is set up. "That exercise gives techs a much better understanding of the inventory they can expect to arrive for reprocessing when the case concludes," says Ms. Apostoles. "It's also a great opportunity for them to let you know if they'll realistically be able to turn around the sets used during the case in a reasonable amount of time."
As you can see, the benefits of streamlined instrument care aren't limited to the SPD. "Consolidating instrument sets decreases overall reprocessing cycle times, which impacts your bottom line from an instrument and consumable perspective, and with respect to total case volumes," says Ms. Apostoles. "The ability to reprocess instruments in a more efficient manner can translate into adding revenue-producing procedures and the opportunity to provide more patients with high-quality care."