Gargantuan freestanding sterile processing facilities are becoming a thing. Just this year, Ohio State University and Penn Medicine unveiled stand-alone facilities. This trend should give surgical facilities more real estate to serve additional patients while also providing sterile processing departments the square footage they need to perform their critical functions in the most efficient ways possible. Facilities leaders say these dual victories can be achieved without sacrificing the sterility of the instrument sets while in transit and won't keep OR teams waiting if there's a traffic jam or a snowstorm. We spoke to three facilities that opted to go the freestanding route to provide you with a closer look at the ins and outs of offsite instrument reprocessing.
Stand-alone Sterile Processing Centers
By: Adam Taylor
Published: 4/9/2021
Facilities have begun building offsite operations to clean and sterilize surgical instruments.
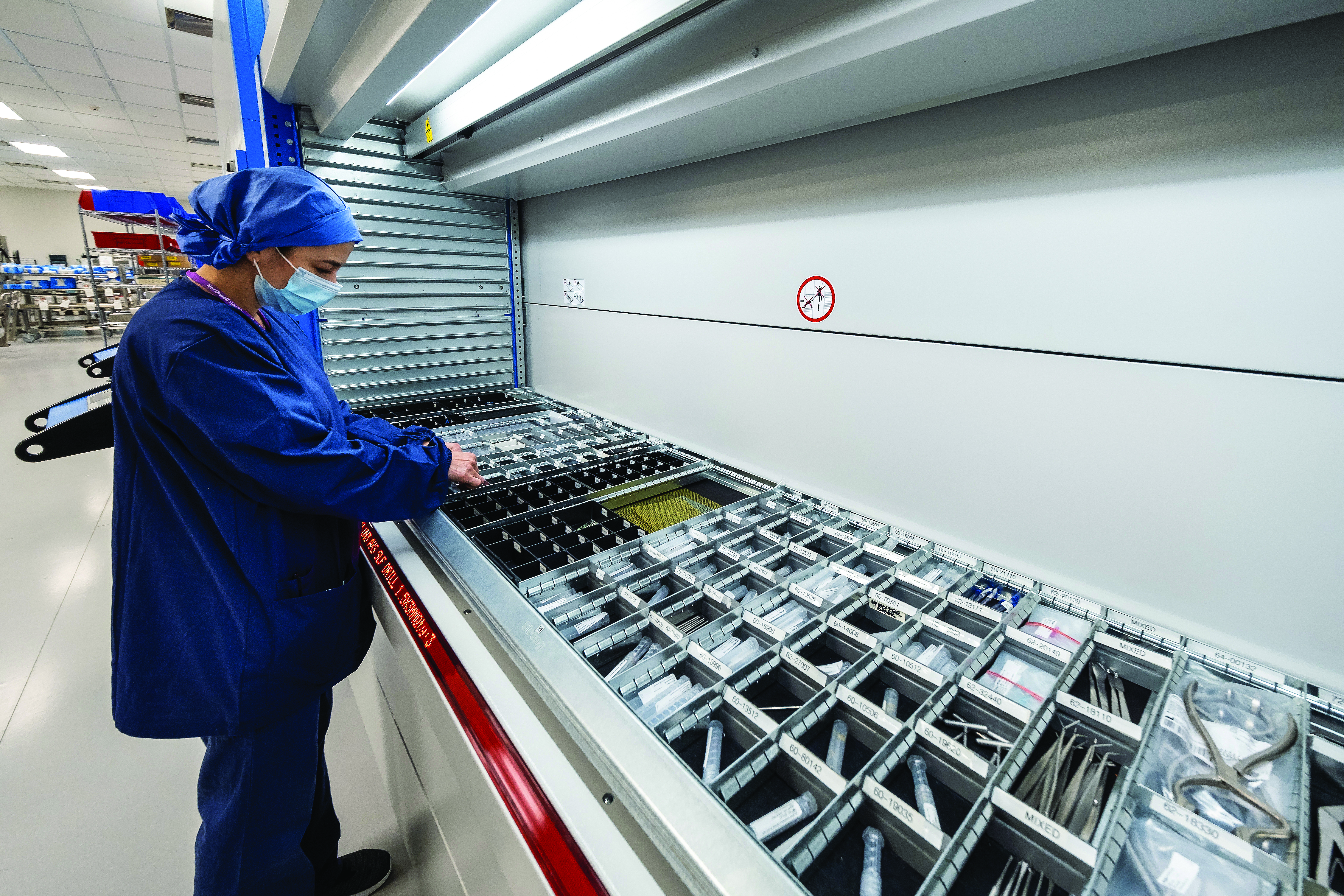
The 110,000-square-foot behemoth
When designing the expansion at the Hospital of the University of Pennsylvania (HUP) in Philadelphia and planning the new HUP East hospital that will open later this year, Penn Medicine officials discovered a space problem. The health system's current sterile processing setup was already less than optimal, with the instrument decontamination area on the fourth floor of one building and the sterilizers in the basement of another. "We were landlocked and realized that performing sterile processing correctly would require nearly an entire floor of the new building, which would be better used for more space to treat patients," says Chris Pastore, managing director of the new sterile processing facility, known as the Interventional Support Center. "That forced us to look at the potential of an offsite model."
The new 110,000-square-foot instrument care facility opened on Feb. 1 — during a snowstorm and with no weather- or transportation-related delays in deliveries, which are 15-to 30-minute drives, says Mr. Pastore. The facility has the capacity to process instruments from up to 200 surgical cases a day, and currently serves HUP, Pennsylvania Hospital and three affiliated outpatient facilities.
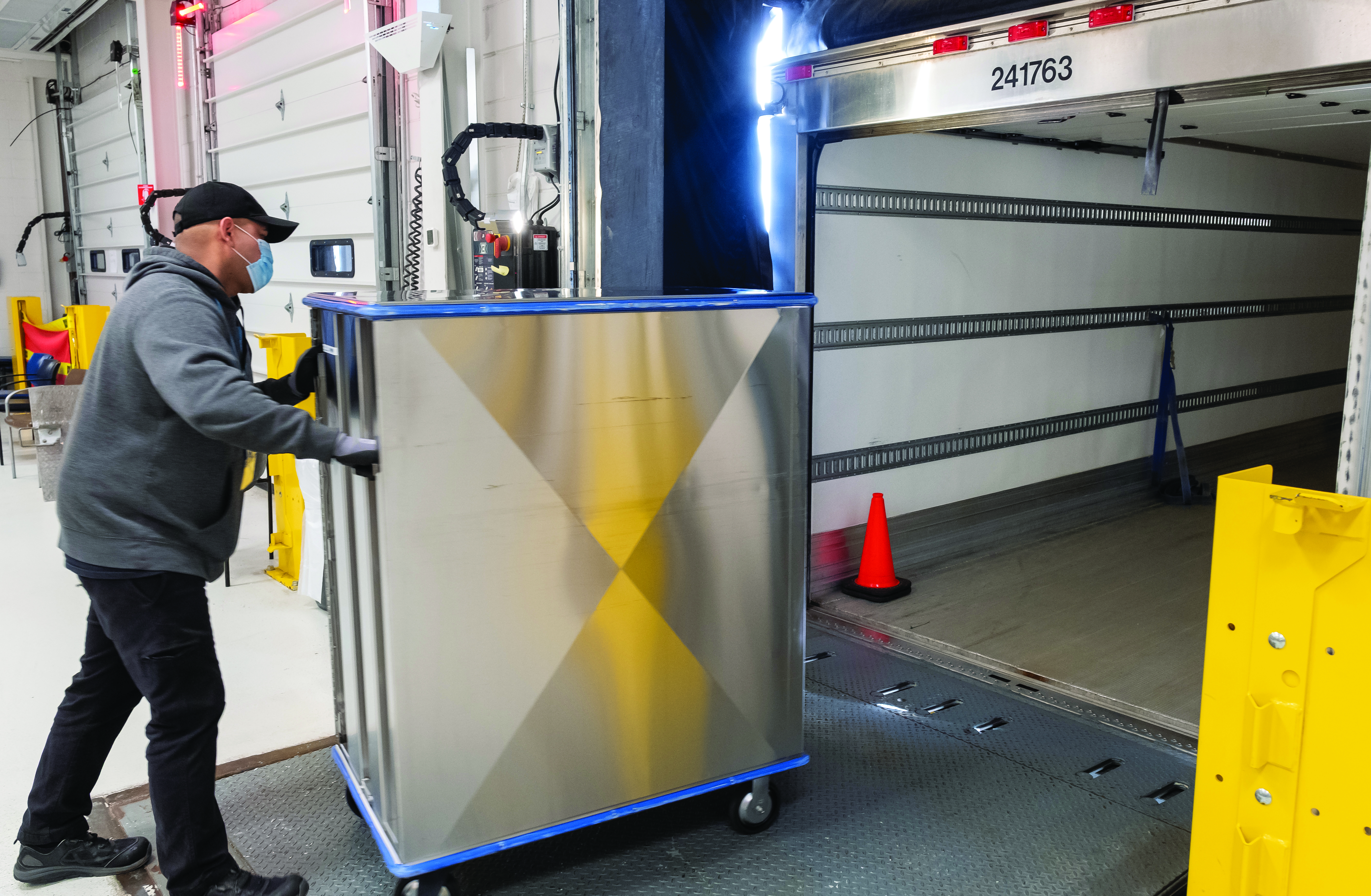
About 140 sterile processing workers moved from Penn Medicine's hospitals and outpatient centers to the new facility and 25 new employees were hired as well. Smaller sterile processing operations remain at all individual locations for fragile ophthalmology instruments and some flexible endoscopes that must be reprocessed within an hour of being used, says Mr. Pastore.
The facility's size allows for a one-way forward-flow approach, so instruments never have to be placed in a container and transported through a "dirty" section of the facility to get to the next clean area in the reprocessing pathway. Instruments are sterilized with clean steam using reverse osmosis water that prevents water residue from remaining on instruments, which could increase infection risks and corrode the surgical sets over time. Airlocks throughout the building also prevent cross-contamination of air between areas where dirty instruments are processed and clean ones are repackaged, and also provide a place for workers to gown and de-gown before going to different areas of the facility. The sinks and tables are adjustable to be ergonomically sound for workers of all heights. Increased air changes and filtration systems minimize dust that could collect on instruments.
The facility also serves as a major prep site for much of the health system's soft goods such as gowns, towels, filters, and gauze. (Gear such as gloves, sutures, screws and implants are kept at the hospitals.) The staff begins picking cases and preparing the soft goods throughout the day before for the next day's surgeries. They go to the facility's "supermarket," which includes a series of rotomats — huge storage carousels similar to garment conveyors at a dry cleaner. Employees plug in a number for an item and the multi-level vertical units with dozens of shelves on each level spin around and deliver it to the prep workers.
Considering that poor communication between OR teams and sterile processing departments has long been known to create problems that result in missing instruments in sets, Penn Medicine has installed an OR nurse to spend half their time at the reprocessing facility to work on regulatory and quality issues. For now, daily 7:30 a.m. virtual huddles are held that include perioperative leaders and directors of nursing because the offsite reprocessing process is less than two months old.
Much of the facility's equipment, such as three-basin sinks and washer disinfectors, are the same as what existed in the onsite sterile processing departments, but there are more of them in the new space. That scale helps. "We have 10 steam sterilizers now. If we needed to do preventative maintenance on one in a hospital, it was an issue," says Mr. Pastore. "Here, I can take one down and still have nine more online, so operations aren't impacted."
Buckeyes lead the way
The Ohio State University Wexner Medical Center opened its freestanding facility, the first of its kind in the state, on Feb. 22. The $45.3 million, 62,000-square-foot space has the capacity to process instruments for 48,000 surgical patients per year. It services four hospitals, multiple same-day surgery centers and will reprocess instruments for at least three new surgery centers within three to five years.
"Surgery is the moneymaker for most health systems, and central sterile is the lifeblood of surgery."— Kim Jones, director of central sterile supply
In addition to instrument reprocessing, the facility will also prepare and pack supplies for cases. It also has an onsite service to repair, refurbish and maintain instruments, as well as administrative offices, conference rooms and staff changing areas.
Kim Jones, OSU Wexner's director of central sterile supply, says the facility was designed to ensure one-way workflow. "Current operations at many older facilities force you to work around structures that prohibit a one-way flow," she says, "but the linear construction at new freestanding facilities ensure every instrument moves from a dirty area to a clean area."
Some of the keys to the success of the new facility included making sure surgeons' preference cards were accurate, says Ms. Jones, so that an instrument a surgeon would need in an hour or two doesn't wind up on a truck to the offset reprocessing facility. The staff created a list of items that would always stay onsite at the health system's hospitals for reprocessing, such as tools that are used in trauma cases. They also worked closely with OR teams at different hospitals to standardize sets used for cases that are turned over with high frequency.
"Surgery is the moneymaker for most health systems, and central sterile is the lifeblood of surgery," says Ms. Jones. "You're working against the grain if your ORs and central sterile departments don't have a strong sense of partnership, cooperation and teamwork."
Instrument sets needed for early morning cases arrive at least a day before the scheduled procedures in which they'll be used, says Ms. Jones. Transport trucks make runs to or from facilities every two hours. The workflow is easier at the outpatient centers than the hospital settings, as the procedures are scheduled in advance and take place between 7 a.m. and 5 p.m.
"We collect instruments immediately and get them sterilized and ready for re-use the next day," says Ms. Jones. Any item used after 7:30 p.m. stays behind and is processed at the facility itself. Staff members at the offsite reprocessing facility work closely with perioperative leaders, so they know exactly what instruments will be arriving for reprocessing and which need to be shipped back to the ORs.
A single large instrument reprocessing location also makes for maximum efficiency. There are eight sinks in the decontamination area, for example, so multiple techs can clean instruments simultaneously. Transport trucks arrive every four hours, so the techs know what instruments are coming and when they'll arrive. As soon as one of the facility's managers finds out what's arriving on the truck, they assign the appropriate number of techs to the decontamination area. When they're finished in decontam, they de-gown and start assembling clean sets, without any of waiting around. "We basically move our staff to where the work is, and they push the instrument through," says Ms. Jones.
The new facility is a good business model — and a tool for staff satisfaction as well. "The folks that have spent their careers in the basement of hospitals now work in an environment with natural lighting and beautiful surroundings," says Ms. Jones. "You can tell it's enhanced the quality of their work lives just by seeing their faces."
The facility that never sleeps
Northwell Health's $80 million reprocessing center on Long Island opened in 2018 at the site of a former popcorn factory that made the snack for movie theaters in the tri-state area. It serves multiple hospitals and outpatient surgery centers in the massive New York health system. The 110,000-square-foot facility processes instruments from 250 to 300 cases a day — about 15 million instruments each year for five hospitals. The facility was built to process 22 million instruments annually over the next several years. It also has on-site technicians who can repair broken instruments and perform preventive maintenance on sets.
Transport workers in trucks pick up instruments in Northwell's hospitals as late as 11 p.m. and deliveries of other batches for the next day's cases starts at 4 a.m. When the instruments for an OR's first case of the day are sterilized and delivered varies. "There's no science to that," says Adam Boll, Northwell's executive director of joint venture operations. "Sometimes the trays may have been there for two days beforehand because it wasn't used. Sometimes the instruments come the night before. Sometimes there may be things that arrive at 4 a.m. for that day."
Regardless of whether you visit the center in the wee hours of the morning or the dead of night, you're guaranteed to find a hub of activity. "We run an intricate, flexible and versatile 24/7 operation," says Mr. Boll. "The reprocessing equipment never stops humming, and our trucks never stop rolling." OSM