It requires cooperation, data, sponsors, champions and persuasion.
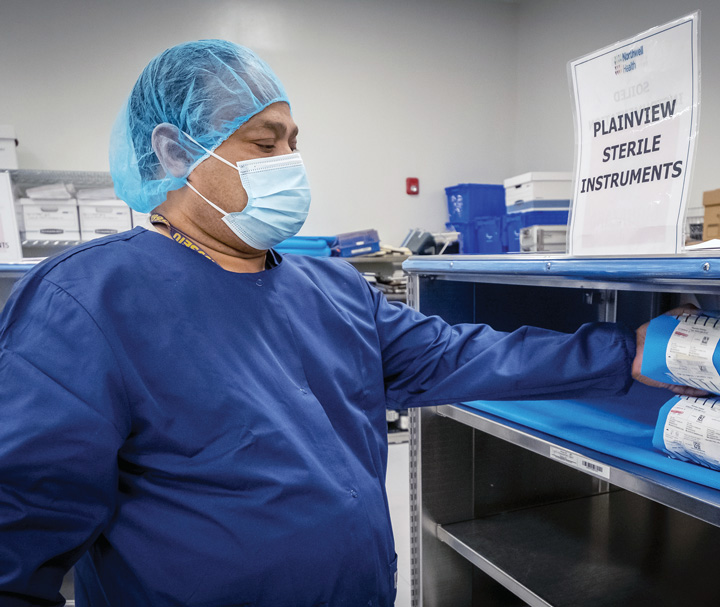
Just how many instruments on the trays in your ORs and procedure rooms are actually necessary? Removing little-used instruments can result in significant savings of time, space, labor and money.
"Your sterile processing techs are likely spending time and effort reprocessing countless instruments that aren’t even used during procedures," says Casey Czarnowski, BA, CRCST, CSPDT, CIS, CER, a sterile processing consultant based in Rochester, Minn. "Your nurses and surgical techs are likely preparing instruments for use that are rarely if ever actually used, cluttering back tables and wasting valuable time."
Mr. Czarnowski, who has seen instrument reduction projects both fail and succeed, offers these tips for success.
Achieve comprehensive buy-in. First, speak with your sterile processing leaders and techs to learn how much unnecessary instrument reprocessing they do, and the wasted time and resources it consumes. Do the same with your surgical techs and OR nurses who set up and handle instrument sets. Then take your case to the C-suite to find a sponsor to endorse the project.
"Your chief nursing officer or chief financial officer are great candidates," says Mr. Czarnowski. The sponsor should approach your chief medical officer to stress that the surgeons need to be involved. "Now everybody's talking, and you have sponsorship and transparency within the C-suite," he says. "Considering this project will likely take months or even a year, that’s crucial for success."
Secure surgeon champions. These surgeons can both help prove the concept and gain peer support and cooperation. "Surgeons are creatures of habit who want every conceivable base covered during a procedure, with every instrument they could possibly need sterile and available to them at all times," says Mr. Czarnowski. "The key is to acknowledge that their concerns are legitimate, but can be addressed in a much better, more productive way. By paring down their instrument set lists, they actually will be served better and faster in the long run because their nurses, surgical techs and reprocessing techs won’t need to handle and inspect hundreds of redundant or unnecessary instruments, only a fraction of which are actually used regularly. Sterile processing will be able to turn core instrumentation around more quickly, while rarely-used instruments will be sterilized and stored, available for rapid delivery."
Pilot with your surgeon champions. "Don't try to do it with every surgeon at once," says Mr. Czarnowski. "Partner solely with your surgeon champions who already understand and embrace the concept." The pilot program should run over the course of several months to generate enough supporting data. "Without testing, data and testimonials from the satisfied surgeons in your pilot project, you'll struggle to get uphill with the rest of your surgeons," he says. "Encourage the surgeons in your successful pilot to talk with their peers about it: ‘Here's what I've done, and it's really great.’"
Your sterile processing department will also now possess valuable data, including improvements in turnaround times, same-day usage of instruments, productivity and efficiency. All of the data you generate will confirm both to the C-suite and other surgeons that a facility-wide instrument reduction effort is worthwhile.
Get the OR and sterile processing on the same page. The big concern of surgeons and their teams will be not putting patients at risk. "If they reduce the set list, will they be able to access rarely used instruments on demand?" says Mr. Czarnowski. "Sterile processing must be able to confidently answer this question. The good news is that you’ve completed your successful trial of the concept with your pilot project — and sterile processing delivered. Because the sets are smaller, sterile processing can better turn around regularly used instruments, while instruments removed from regular rotation are in sterile storage and ready whenever needed, rather than unavailable because they’re going through another unnecessary reprocessing cycle."
Address storage. Reevaluate all storage space with your C-suite sponsors to see whether it needs to be expanded to better ensure consistent sterility of the increased number of instruments removed from regular rotation. Reduce the potential for holes in blue wrap, broken locks or punctured pouches that require instruments to be reprocessed again before use.
"Two or three years down the line, the payoff if your instrument reduction program succeeds is that you will have fewer and smaller instrument sets you’ll need to store," says Mr. Czarnowski. "You might even be able to get rid of some redundant sets and instruments."